Syntheseöle – rechnet sich ihr Einsatz wirklich?
Heute wird kaum noch ein neues Fahrzeug ausgeliefert, dessen Motor nicht bereits im Werk mit einem niedrigviskosen, vollsynthetischen Öl befüllt wurde. Auch in der Industrie werden immer häufiger Syntheseöle eingesetzt. Typische Beispiele sind Hydraulikflüssigkeiten für Baumaschinen oder Hochleistungs-Getriebeöle für Windkraftanlagen, aber auch Spezialprodukte, wie Hochtemperatur-Kettenöle oder Umlauf-Schmieröle für Papiermaschinen.
Vollsynthetische Schmierstoffe werden auf der Basis von Kohlenwasserstoffen hergestellt. Ausgangsprodukte können sowohl Erdölprodukte als auch verschiedene andere Rohstoffe sein, aus denen Kohlenwasserstoffe gewonnen oder synthetische Fluide hergestellt werden können. Bei der Produktion werden die Molekülstrukturen so verändert, dass sich die gewünschten Schmiereigenschaften ergeben und sich die optimale Viskositätslage einstellt. Entsprechende Additive werden zugemischt, die für die meisten synthetischen Öle nahezu identisch mit denen für mineralölbasische Grundöle sind. In der Regel sind synthetische Produkte zwar um ein Mehrfaches teurer als die gleiche Menge mineralölbasischer, doch ihre Vorteile sind nicht von der Hand zu weisen.
Inhaltsverzeichnis
Niedrigere Energieverluste, besserer Wirkungsgrad
Syntheseöle sind bei gleicher ISO-Viskositätsklasse und niedrigen Temperaturen deutlich „dünner“ als konventionelle Mineralöle. Eine Einheit, die diese „Mehrbereichscharakteristik“ deutlich werden lässt, ist der Viskositätsindex (VI). Dieser liegt bei mineralölbasischen Schmierölen meist im Bereich von 90 – 100, während er bei synthetischen Grundölen fast immer über 140 liegt. Je höher der VI, desto weniger Energie wird bei gleicher Nominalviskosität beim Kaltstart oder bei niedrigen Umgebungstemperaturen benötigt. Da solche Öle leichter fließen, verbrauchen sie durch reduzierte Plantsch-und Pumpverluste weniger wertvolle Energie.
Syntheseöle helfen also dabei, Kraftstoff oder elektrische Energie zu sparen. Dies umso mehr, je niedriger die Temperatur ist. Durch die gezielte Einstellung der Molekülstruktur werden mit Syntheseölen auch ohne spezielle Additive, wie z. B. „friction modifier“, niedrigere Reibwerte erzielt. In der Praxis lassen sich daher mit Syntheseölen nicht nur aufgrund der Viskositätslage, sondern auch dank ihrer ausgewogenen Formulierung, zwischen 0.5 und 3% Energie einsparen.
Das Einsparungspotenzial kann je nach Anlage erheblich sein. Der Einsatz der oft wesentlich teureren Syntheseöle macht sich auf Dauer alleine durch das Energie-Einsparpotenzial mehr als bezahlt. Kalkulieren Sie für Ihre Anlagen, wie hoch Ihre Energiekosten sind und welchen Spareffekt Sie in Ihrem Betrieb erzielen können.
Längere Öllebensdauer
Wird ein Öl eingesetzt, altert es mit fortschreitendem Gebrauch. Reaktionen der Ölmoleküle z. B. mit Sauerstoff lassen Öle dabei oxidieren. Mit speziellen Additiven, den „Antioxidantien“, lässt sich der Oxidationsprozess deutlich verlangsamen.
Auch Syntheseöle sind nicht vom Alterungsprozess ausgenommen. Doch sie weisen in der Regel deutlich längere Standzeiten auf als Mineralöle. Die Alterung einer Ölfüllung wird, besonders im Industriebereich, durch die Einsatzzeit und die Temperatur, die das Öl während seiner Verwendung erfährt, erheblich beeinflusst.
Daneben wirken Verunreinigungen wie Wasser, Staub oder Verschleißpartikel beschleunigend auf das Oxidationsverhalten eines Öls ein. Die Öloxidation und der in Gebrauchtöl noch vorhandene Gehalt von „Antioxidantien“ lassen sich nur mit Hilfe von aufwändigen Laboranalysen mittels Infrarot-Spektroskopie oder mit dem RULER feststellen.
„Schlechter Geruch“ alleine ist noch kein Zeichen für Ölalterung. Nahezu alle Öle enthalten zur Reduzierung von Verschleiß auch Schwefelverbindungen, deren Zersetzungsprodukte wie nach „faulen Eiern“ riechen und die den „ranzigen“ Geruch, wie er bei der Ölalterung entsteht, deutlich überdecken.
Im Gegensatz zu Mineralölen weisen Syntheseöle keine „Fehlstellen“ in der Molekülstruktur auf, an denen Sauerstoff angreifen und so die Alterung initiieren kann. Syntheseöle haben bereits aufgrund der Gleichförmigkeit der Moleküle und der in Bezug auf Sauerstoffeinfluss stabilen Molekülstruktur eine erheblich bessere Oxidationsstabilität als ein gleich additiviertes Mineralöl. Zusätzlich wird die Oxidationsneigung von Syntheseölen mit modernen Antioxidantien auf der Basis von Phenolen, Aminen oder Salizilaten noch so lange unterbunden, bis dieser Alterungsschutz verbraucht ist.
Deshalb können Syntheseöle oft um ein Mehrfaches länger im Einsatz bleiben als Mineralöle. Nur wenn Syntheseöle, wie im motorischen Betrieb, stark durch Verbrennungsrückstände verunreinigt oder mit mehr als 5% Mineralöl vermischt werden, sinkt die Alterungsstabilität.
Formel für die Ölalterung von Mineral- und Syntheseölen
Wie Pflanzenöl in Abhängigkeit von Temperatur und Zeit ranzig wird, so altert auch das in Urzeiten aus Pflanzen entstandene Mineralöl.
- Als Faustformel für die Geschwindigkeit der Ölalterung hat sich für nicht vermischte und verunreinigte Mineralöle bewährt:
Alle 10°C über einer Temperatur von 50°C verdoppelt sich die Geschwindigkeit der Ölalterung. Geht man davon aus, dass ein gut ausraffiniertes Mineralöl, wie es z. B. für die Herstellung von Turbinenölen eingesetzt wird, bei 50°C mindestens 40.000 Stunden im Einsatz bleiben kann, so reduziert sich diese Zeit bei 60°C auf 20.000 Stunden und bei 70°C auf 10.000 Stunden.
- Beim Einsatz von Syntheseöl liegt nicht nur die Temperatur für den Beginn der Ölalterung höher, auch die Geschwindigkeit der Ölalterung verlangsamt sich deutlich. So kann für ein nicht verunreinigtes und unvermischtes Syntheseöl von folgender Faustformel ausgegangen werden:
Alle 15°C über 60°C halbiert sich die zu erwartende Öllebensdauer. Ein synthetisches Hydrauliköl, wie es in Baumaschinen eingesetzt wird, kann z. B. bei Temperaturen im Hydrauliktank von 60°C immerhin 40.000 Stunden im Einsatz bleiben. Bei 75°C halbiert sich diese Zeit auf 20.000 Stunden. Bei 90°C, einer Temperatur, bei der heute viele Anlagen betrieben werden, kann das Öl immerhin noch 10.000 Stunden eingesetzt werden. Bei Baumaschinen ist dies quasi eine Lebenszeitfüllung.
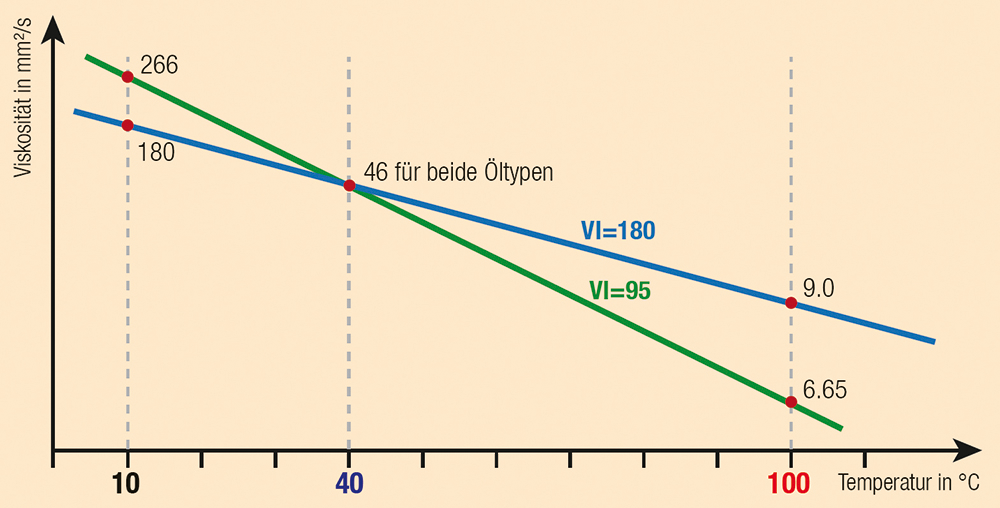
Ölalterung und Öllebensdauer im Vergleich
Temperatur °C beim Einsatz von Mineralöl | Betriebstunden, die das Öl ohne Ölwechsel überstehen kann | Temperatur °C beim Einsatz von Syntheseöl |
---|---|---|
50 | 40.000 | 60 |
60 | 20.000 | 75 |
70 | 10.000 | 90 |
80 | 5.000 | 105 |
90 | 2.500 | 120 |
100 | 1.250 | 135 |
110 | 625 | 150 |
120 | 312 | 165 |
130 | 156 | 180 |
Weitere Vorteile, die für den Einsatz von Schmier- und Betriebsstoffen auf synthetischer Basis sprechen:
- Niedrige Verdampfungsverluste und damit weniger Ölverbrauch im Vergleich zu Mineralölen identischer Viskosität bei Ölsumpftemperaturen von 100°C und darüber.
- Gutes Luftabscheideverhalten senkt die Kavitationsneigung, das Öl ist weniger kompressibel.
- Weniger Luft im Öl reduziert die Ölalterung. Weniger Schaumbildung, weil sich die gleichen Hochdruckeigenschaften mit einem geringeren Gehalt an Additiven, die schaumfördernd sein können, erzielen lassen.
- Gute Filtrierbarkeit, weil keine langkettigen, klebrigen Molekülverbindungen von Zusätzen, mit denen das Viskositäts-Temperatur-Verhalten (VI-Improver) optimiert wird.